Process Development
What are the possible configurations that bioreactors can have?
Stirred-tank designs are probably the most common form of bioreactor, and they share several consistent design features with specific modifications that support a particular bioprocess. The main body of a reactor is a cylindrical vessel that contains the cells, culture media, and other components added to the reaction mix.
The most common materials for the bioreactor body are borosilicate glass or stainless steel. Borosilicate glass has the advantage of being highly durable and chemical resistant. Similarly, stainless steel bioreactors are durable and have low reactivity to chemicals and components typically used in bioprocesses. One advantage of stainless steel (generally 316L grade) designs is a greater tolerance to withstanding pressure differences. This pressure tolerance becomes especially important in large-scale vessels, where pressurized steam is used for Sterilization in Place (SIP) between individual bioprocess runs.
Some form of stirring device is required to mix all the culture media components, prevent cells from clumping together or settling to the bottom of the bioreactor, and promote mass transfer.
The agitator’s design should support the system’s overall design characteristics and the intended bioprocess. The agitator’s impeller portion can successfully use several designs, but it will either provide radial flow mixing or axial flow mixing. Radial flow impellers tend to have flat blades, and they will cause liquid flow around the radius of the bioreactor – a circular motion around the sides. Radial flow impellers are most appropriate when gas-liquid mixing or other blending is crucial. Axial flow impellers have pitched blades and will provide liquid flow along the bioreactor axis – flow between the tank’s top and bottom. Axial flow impellers give a gentler but more efficient mixing effect and are suited to bioprocesses with shear-sensitive cells or particles.

The agitator can be powered through a direct or an indirect linkage to a motor. In both cases, the motor is outside the bioreactor’s body. With a direct linkage, the motor is coupled directly to a stirrer shaft, which enters through the reactor vessel’s top or bottom. The impellor is then fixed onto that shaft. The motor is connected to a magnetic driver outside the bioreactor in an indirect linkage. The impeller sits entirely within the reactor vessel and has corresponding magnets that couple to the external driver. With indirect power, the impeller can be fitted to a stirrer shaft (the shaft contains the magnetic coupling), or the impeller can directly include magnets and be shaftless.
A direct coupling has the advantage that it can provide higher stirrer torque, so it is more suitable for viscous mixtures or when cells form mats or clumps. Indirect coupling tends to offer lower torque, and care must be taken to prevent the magnets from decoupling, such as running the stirrer too fast.
Inlets allow the introduction of fluid, such as fresh media, but can also include other sources, such as acid and bases. One of the critical parameters in biological processes is pH. The addition of pH probes in the bioreactor ensures close monitoring of its values and correction when a diversion from acceptable value happens. To correct this value, acids or bases can be added. Although these can all be provided manually, automated systems are commonly used based on either process knowledge or bioprocess monitoring. Automated systems connect inputs from the probes and measurements inside the reactor with specified bioprocess operating set-points with the pumps that will then feed in an appropriate liquid to maintain the optimum conditions.
Solutions
The BioXplorers and their versatility can play essential roles in Process Development. BioXplorers support a range of operational modes, including batch, fed-batch, and continuous reactors. They are highly versatile and allow for a range of measurements as standard, including temperature, pH, dissolved oxygen (DO), foam formation, liquid level, oxidation-reduction potential (ORP), and cell density. To prevent volume loss linked to evaporation, the BioXplorer is equipped with Peltier coolers, avoiding vapor loss through the gas line. This flexibility, combined with its versatile reactor configurations, makes it a dynamic solution in the advancement of bioprocess development. Furthermore, combined with WinISO, it permits the automatization of processes, increasing reliability and diminishing the chances of human error.
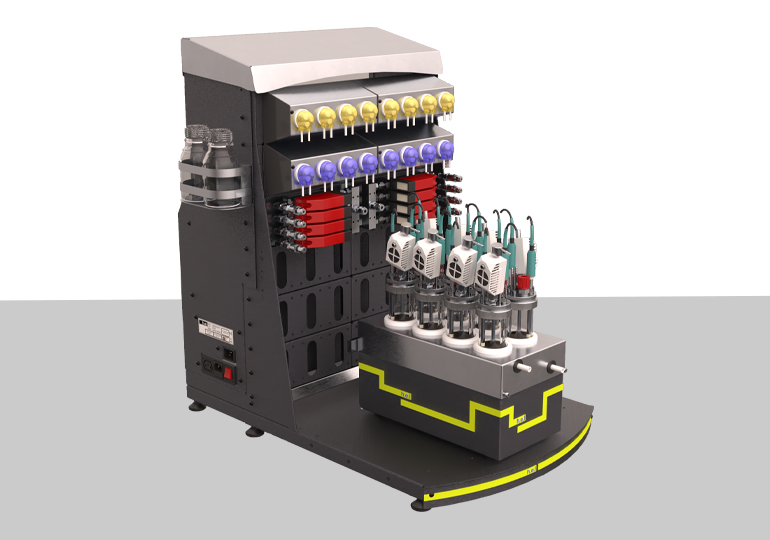
BioXplorer 100 | bench-top, parallel 8 bioreactor platform
The BioXplorer 100 is a multi-bioreactor system designed for the optimization of aerobic f...
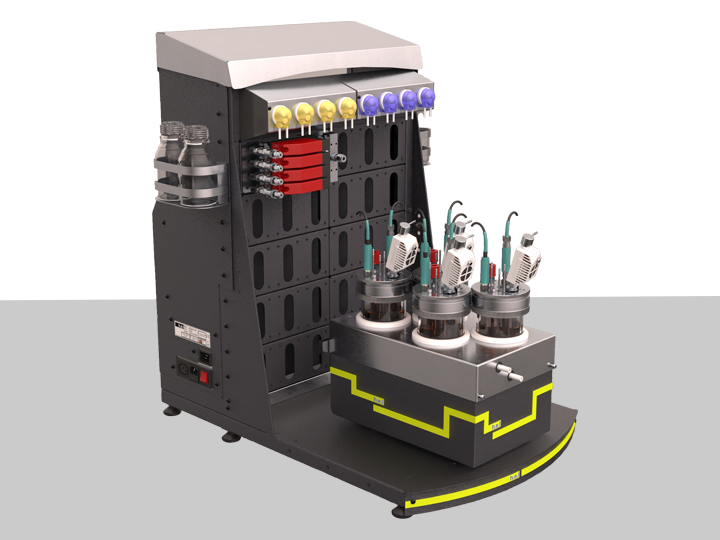
BioXplorer 400 | bench-top, parallel 4 bioreactor platform
The BioXplorer 400 is equipped with 4 bioreactors with working volumes of up to 400 ml. It...
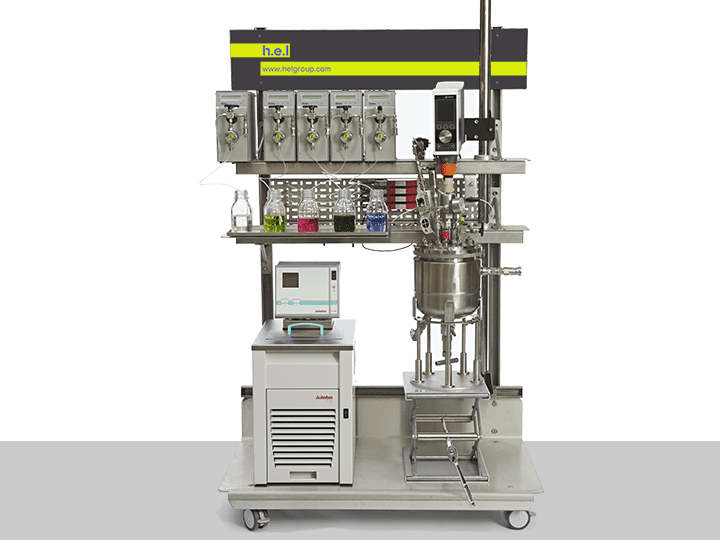
BioXplorer 5000 | Lab-scale bioreactor platform
The BioXplorer 5000 and 5000P single bioreactor systems are ideally suited to drive your s...
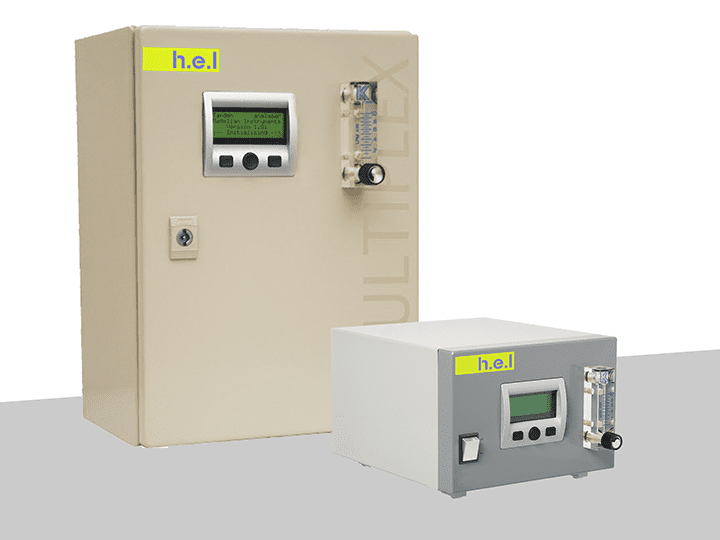
Tandem Off Gas Analyzers | Multi Line and Continuous Systems
The Tandem gas analyzer systems will give you real-time, on-line data that helps you under...
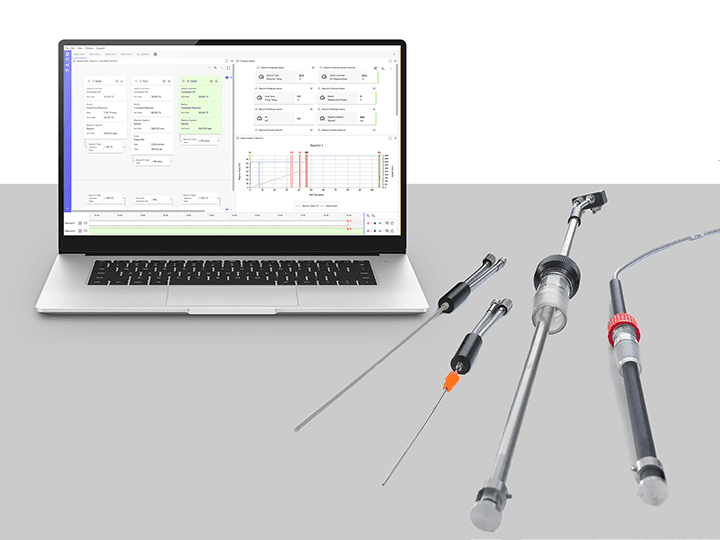
BioVIS | An Inline Cell Density Indicator Sensor
BioVIS is a probe for the inline monitoring of total cell growth and biomass within a bior...
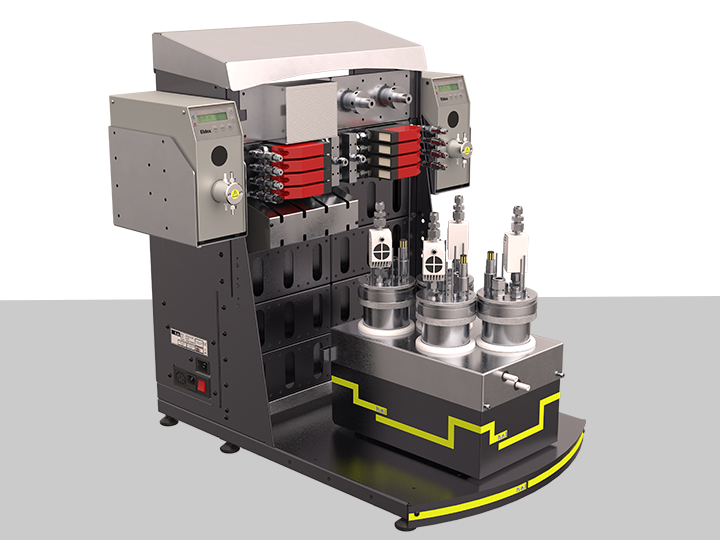
BioXplorer 400P | High-pressure bench-top, parallel 4 bioreactor platform
The BioXplorer 400P is an automated parallel pressure bioreactor system for the discovery ...
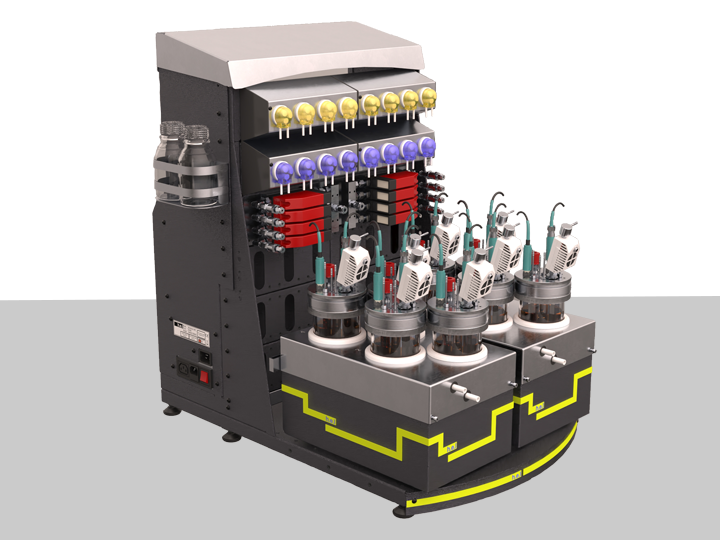
BioXplorer 400XL | Expanded Bench-Top, Parallel 8 Bioreactor Platform
Featuring eight 500 ml bioreactors, the BioXplorer 400XL allows the fast optimization of c...